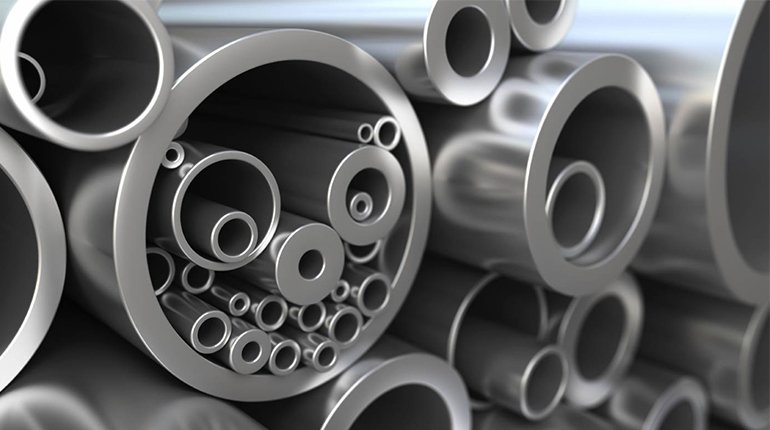
آلیاژ های پایه نیکل
آلياژهاي نيكل به دستهاي از آلياژها كه حاوي نيكل هستند اطلاق ميشود. آلياژهاي پايه نيكل نيز شامل آلياژهايي ميشوند كه قسمت اصلي تشكيل دهنده آنها نيكل ميباشد كه گاهي ممكن است از 50 درصد كمتر باشد.آلياژهاي مس حاوي نيكل براي ساخته اسلحه، ابزار و سكه از ابتداي تمدن بشري به كار ميرفتهاند. اولين آلياژ پايه نيكل مونل ميباشد كه در سال 1905 ميلادي ساخته شد. اين آلياژ استحكام خوب و مقاومت به خوردگي مناسبي در محيطهاي مختلف آبي دارد. سيستم آلياژي نيمونيك كه شامل نيكل، كرم و تيتانيم ميباشد باعث بهبود خواص در دماي بالا ميشود. اين آلياژها پس از مونل به كار رفت، پل مريكا تيتانيم و آلومينيوم را براي ايجاد رسوب سختي در آلياژهاي نيكل به كار برد. آلياژ پر استحكام پيرشونده مونل، K500 در سال 1924 معرفي شد. با افزودن موليبدن به آلياژهاي نيكل در سال 1920 هاستالويهاه آلياژهاي Ni-Mo و Ni-Cr-Mo بودند و مقاومت استثنايي در محيطهاي احيايي داشتند معرفي شدند. آلياژ Fe-Cr-Ni كه اينكونل 600اميده شدند در سال 1931 گسترش يافت. اين ماده در ابتدا براي تجهيزات لبنياتسازي به كار رفت ولي امروزه قسمت اصلي ژنراتورهاي بخار نيروي هستهاي را تشكيل ميدهد. اينكونل هاي پركرمتر مثل آلياژ 690 بعد ازآن معرفي شد و براي اين ژنراتورها مناسبتر بود. به علت كمبود نيكل در سالهاي حدود 1950 آلياژهاي كمنيكل مانند Incoloy alloy 800 معرفي شده و به جاي آلياژ 600 به كار رفتند.
همچنين در دهه 1940 آلياژ نيمونيك 80 و 80A براي كاربرد در هواپيماها ساخته شدند. در ابتدا دهه 1960 و 1970 آلياژهاي اينكونل 718، 625 و 617 با استحكام و مقاومت به خوردگي استثنايي در دماهاي بالا ساخته شدند. با پيشرفت موتور هواپيماها، اين مواد كاربردهاي جديدي پيدا كردند.علاوه بر اين آلياژهاي پايه نيكل خاصي نيز براي استفاده در فرآوري مواد شيميايي گسترش يافتند. در دهه 1950 آلياژ اينكولوي 825 و آلياژ ( carpenrer 20cb-3 (Ni-Cr-Fe-Mo-Cu كه مقاومت به خودرگي آبي خصوصاً در اسيد سولفوريك داشتند گسترش يافتند. در دهه 1970 با پيشرفت روشهاي ذوب آلياژ هاستالوي c-276 كه خلوص بيشتري از هاستالوي C و B-2 داشت و در واقع اصلاح شده آلياژ B بود توليد شد.
در دهه 1980 نياز به مواد مناسب در كنترل آلودگي و صنايع شيميايي باعث توليد آلياژ هاستالوي C-22 شد. در دهه بعدي نيكروفر Nicrofer Alloy 59 توليد شد.اينكونل 686 و هاستالوي C-2000 براي مقاومت به خوردگي در محيطهاي اسيدي اكسيد و احيا كننده با اضافه كردن كرم، مولبيدن، تنگستن يا مس ساخته شدند. افزايش استفاده از آلياژهاي نيكل در توليد گاز طبيعي باعث ساخت آلياژ پراستحكام و پير شونده Incolloy 925 وAlloy 625 شد. آلياژهايي مانند اينكونل 601، هاستالوي 216 و HE-160 مقاومت به اكسيداسيون بهبود يافتهاي در بيشتر كاربردها دارند.
2-آلیاژهای ریختگی نیکل
1-2-نیکل خالص ریختگی CZ-100
آلياژ CZ-100داراي 1% كربن و 2% سيليسيم و مابقی نیکل ميباشد. براي افزايش مقاومت به سايش و تاولزدن ميتوان مقدار كربن و سيليسيم آلياژ را افزايش داد. معمولاً اين آلياژ با 75/0% كربن و 1% سيليسيم ريختهگري ميشود. در صورت صحيحبودن روش توليد گرافيت به صورت كروي در ميآيد. اگر گرافيت به صورت ورقهاي باشد خواص مكانيكي كاهش خواهد يافت. در صورت نياز به جوشكاري مقدار كربن موجود را بايد به 1/0 درصد يا كمتر محدود كرد. در اين صورت ريختهگري آلياژ كمكربن مشكلتر خواهد شد ولي تأثيري بر كاركرد قطعه ندارد. اين آلياژ چقرمگي عالي، مقاومت حرارتي و هدايت حرارتي خوب دارد .
اين آلياژ براي جابجايي مواد خورندهاي مانند قلياها و يا جاهايي كه نياز به عدم آلودگي مواد به عناصري مانند مس و آهن باشد استفاده ميشود. دماي ليكوئيدوس اين آلياژ 1425 تا c ْ1460، دماي ساليدوس 1360 تا c ْ1410 و دماي ذوب تقريبي آن c ْ1345 ميباشد. دماي ريختهگري CZ-100 براي ريختهگري در ماسه 1510 تا c ْ1595 ميباشد.
2-2- نيكل – مس
مطابق استاندارد A494 آلياژهاي اين گروه M-35-1 ، M-35-2 ، M-30H ، M25S و M-30C ميباشند. آلياژهايي كه سيليسيم كمتر از 2% معمولاً همراه با آلياژهاي نيكل – مس و مس – نيكل كار شده در پمپها، والوها و اتصالات ريختگي جهت مقاومت به خوردگي به كار ميروند.
گروهي كه بيشتر از 2% سيليسيم دارند، علاوه بر مقاومت به خوردگي، استحكام بالا و مقاومت به سايش خوبي نيز دارند. وقتي مقاومت به تاولزدگي مدنظر باشد مقدار سيليسيم بيشتر از 4% خواهد رسيد. خصوصيات كششي آلياژ ريختگي نيكل – مس با تأثير سختي محلولي سيليسيم يا سيليسيم و نيوبيم كنترل ميشود. خصوصيات كششي M-35-1 و M-35-2 توسط رابطه كربن و سيليسيم و آلياژ M-30C و E توسط رابطه سيليسيم و نيوبيم مشخص ميشود.
حدود 5/3% سيليسيم باعث ايجاد خاصيت پيرسختي در اين آلياژ خواهد شد. وقتي مقدار Si از حلاليت سيليسيم در زمينه نيكل مس زيادتر شود (3/8% سيليسيم) فاز ترد و شكننده سيليسايد تشكيل خواهد شد. خاصيت پيرسختي و وجود سيليسايدها در آلياژ D باعث مقاومت استثنايي در برابر تاول زدن خواهد شد. چقرمگي آلياژهاي نيكل– مس با افزايش مقدار سيليسيم كاهش مييابد ولي همة آلياژها در دماهايC ْ195- تا دماي محيط چقرمگي خود را حفظ ميكنند
آلياژ M-35
آلياژ M-35 براي كاربردهايي كه نياز به استحكام بالا، نشتناپذيري و مقاومت به فعاليتهاي شيميايي مخرب و سايش مكانيكي داشت باشند به كار ميرود. دماي ذوب اين آلياژ بين 1315 تا ْ1345 ميباشد كه بستگي به تركيب شيميايي آلياژ دارد. دماي ريختهگري مناسب براي M-35 حدود 1480 تا c ْ1565 ميباشد.
براي جوشكاري اين آلياژ با روش الكترود دستي (SMAW) بهتر است از الكترود ENiCu-1 يا ENiCu-2 و جريان مستقيم قطب معكوس DCRP استفاده شود. معمولاً براي اين آلياژ از عمليات پيشگرم و پسگرم استفاده نميشود.
مونل H يا M-30H
اين آلياژ به علت مقاومت به تاولزدگي و خوردگي، سختي نسبتاً بالا قابليت و ماشينكاري متوسط در صنايع استفاده ميشود. دماي ذوب آلياژ 1285 تا c ْ1315 ميباشد. در 1315 تا c ْ1455 ريختهگري ميشود. براي اكسيژنزدايي مذاب اين آلياژ از منيزيم استفاده ميشود.
مونل S يا M-25S
اين آلياژ داراي مقدار سيليسيم زيادتر ميباشد. نقطه ذوب آلياژ حدود 1260 تا c ْ1290 است و در دماي 1455 تا c ْ1540 ريختهگري ميشود. براي اكسيژنزدايي اين آلياژ نيكل – مس نيز از منيزيم و آلياژهاي آن استفاده ميشود. براي نرم كردن اين آلياژ قطعات ابتدا به مدت يك ساعت در c ْ870 گرم ميشوند و سپس تا c ْ650 در هوا سرد شده و از اين دما تا دماي محيط كوئنچ ميشوند. براي سختكردن قطعات در دماي c ْ595 به مدت 4 تا 6 ساعت گرم شده و سپس در هوا يا كوره سرد ميشود
3-2- نيكل – كرم – آهن
آلياژ CY-40 نيز در استاندارد A494 مشخص شده است. مقدار كربن، منگنز و سيليسيم آلياژ ريختگي اين آلياژ بيشتر از آلياژ كار شده است. افزايش اين عناصر باعث افزايش قابليت ريختهگري و آببندي بهتر قطعات تحت فشار ميشود. آلياژهاي نيكل – كرم – آهن مقاوم به حرارت مانند HX و HW در استاندارد A297 ذكر شدهاند. HW آلياژ 60 درصد نيكل، 12 درصد كرم و 23 درصد آهن ميباشد. در جايي كه مقاومت خوبي به كربوره و اكسيدشدن در دماي بالا دارد و در جايي كه نوسانات دمايي وجود داشته باشد قابل كاربرد است.
اين آلياژ در ساخت فيكسچرهاي عمليات حرارتي كه براي كوئنچ به كار ميروند و تجهيزات كورهها كه تحت تنش و شوكهاي حرارتي هستند استفاده ميشود. در صورتي كه در محيط محصولات حاصل از سوختن گوگرد نداشته باشند اين آلياژ تا دماهاي بالا c ْ1040 قابل استفاده ميباشد.
ساختار آلياژ HX داراي زمينه استنيتي با كاربيدهاي پراكنده در آن ميباشد. مقدار و اندازه كاربيدها در ساختار بستگي به مقدار كربن و سابقه گرمايي قطعه دارد. اگر قطعه زمانهاي طولاني در دماي بالا استفاده شده باشد ذرات كاربيد زياد خواهند بود. تغيير ساختار باعث افزايش استحكام در دماي محيط ميشود ولي تأثيري بر انعطافپذيري ندارد.
آلياژ HX مشابه HW با مقدار نيكل بيشتر (66Ni-IVe) ميباشد. كرم بيشتر در اين آلياژ باعث مقاومت به خوردگي داغ حتي در گازهاي گوگرددار ميشود و تا دماي c ْ1150 قابل كاربرد ميباشد.
آلياژ CY-40 (Inconel 600) براي ساخت اتصالات ريختگي متصل به آلياژهاي كار شده با تركيب شيميايي مشابه استفاده ميشود. جدول خصوصيات مكانيكي اين آلياژ در جدول 1-21 آمده است. نقطه ذوب اين آلياژ 1370 تا c ْ1400 و دماي ريختهگري آن1540 تا c ْ1620 ميباشد. براي اكسيژنزدايي اين آلياژ معمولاً از آلياژهاي حاوي منيزيم استفاده ميشود. رنگ ظاهري اين آلياژ سفيد ميباشد .
4-2- نيكل – كرم – موليبدن
وقتي دماي بالا و اسيد در محيطي وجود داشته باشد از اين دسته آلياژها مانند CW-12MW ، CW-7M ،CW-ZM و CW6M استفاده ميشود. موليبدن موجود در آلياژها باعث افزايش استحكام دماي بالا و مقاومت به اسيدهاي غيراكسيدكننده ميشود.
آلياژهاي CW-12MW و CW-7M تنش تسليم دماي بالاي خوبي دارند كه به علت تأثير سختي محلولي كرم، موليبدن و سيليسيم و CW-7M و تنگستن و واناديم در CW-12MW ميباشد. انعطافپذيري اين آلياژها تا حد محلوليت جامد عالي ميباشد. هر چند عمليات حرارتي يا بالانس نادرست عناصر آلياژي ميتواند باعث افت شديد انعطافپذيري شود در آلياژهاي اين گروه بايد مقدار كربن و گوگرد را تا حد امكان پايين نگهداشت.
آلياژ CW-12MW(Hastelloy C276)
از اين آلياژ براي ساخت تجهيزات فرآوري مواد شيميايي استفاده ميشود. در صورتي كه اسيد نيتريك يا هيدروليك داراي نمكهاي فلزي باشند و دماي استفاده بالاتر از c ْ50 باشد اين آلياژ به جز براي محلولهاي ضعيف قابل استفاده نميباشد.
دماي ليكوئيدوس اين آلياژ 1340 و دماي ساليدوس آن c ْ1265 ميباشد. اين آلياژ در برابر عاملهاي اكسيدكنندهاي مانند كلرتر، گاز كلر، هيپوكلريت، محلولهاي دياكسيد كلر، كلريد و نيتريك فريك، هيدروكلريد و اسيد سولفوريك در دماهاي متوسط و شرايط اكسيدكننده، اسيداستيك، آب دريا نمكها و اسيدهاي خورنده آلي مقاومت خوبي دارد. تا دماهاي c ْ1090 در محيطهاي اكسيد و احيا كننده ميتوان از اين آلياژ استفاده نمود. اگر اين آلياژ به مدت طولاني در 500 تا cْ800 قرار گيرد. نرخ خوردگي آن زيادتر ميشود و در اين صورت بايد قطعات مجدداً آنيل شوند.
عمليات حرارتي محلولي براي CW-12M-1 در دماهاي 1180 تا c ْ1230 انجام ميشود و بعد از آن توسط فرو بردن در آب يا اسپري آب سرد كردن انجام ميشود.
براي جوشكاري اين آلياژ جوشكاري گاز و قوس كربن پيشنهاد نميشوند. در قوس الكترود دستي SMAW با استفاده از الكترود AWS ENiCrMo-4 يا ENiCrMo-5 جوشكاري با جريان مستقيم قطب معكوس (DCRP) جوشكاري انجام ميشود .
5-2- نيكل – موليبدن
آلياژهاي (Hastelloy B) N-12MV و(Hastelloy B2) N-7M از استاندارد A494 در اين رده قرار ميگيرند. اين آلياژها بيشتر در حمل و نقل اسيد هيدروكلريك در دماها و غلظتهاي مختلف تا نقطه جوش استفاده ميشوند. اين آلياژها به علت سختي محلولي موليبدن داراي استحكام تسليم خوبي هستند. در انعطافپذيري اين آلياژها مقدار كربن و موليبدن نقش اساسي دارند. براي ايجاد حداكثر انطعافپذيري، مقدار كربن بايد تا حد امكان كم باشد. مقدار موليبدن موجود در آلياژ نيز بايد به صورت تنظيم شود كه فازهاي بين فلزي تشكيل نشوند.
آلياژ N-12M
از اين آلياژ در ساخت تجهيزات صنايع شيميايي و كاربردهاي دماي بالا استفاده ميشود در محيطهايي كه اسيد يا نمكهاي اكسيدكننده قوي وجود دارند نبايد از اين آلياژ استفاده شود. در محيطهاي اكسيد كننده حداكثر دماي كاري c ْ760براي اين آلياژ در نظر گرفته شده است ولي در اتمسفرهاي احيايي ميتوان از اين آلياژ در دماهاي بالاتري نيز استفاده نمود.
دماي ليكوئيدوس اين آلياژ 1370 و دماي ساليدوس آن c ْ1300 ميباشد. دماي ريختهگري مناسب براي اين آلياژ c ْ1450 است كه بايد قطعه به سرعت سرد شود. عمليات محلولي اين آلياژ در دماي c ْ1177 براي N-12M-1 و c ْ1120 براي N-12M-2 و سرد كردن سريع يا كوئنچ انجام ميشود. اين عمليات باعث ايجاد حداكثر انعطافپذيري،مقاومت به خوردگي و قابليت ماشين كاري ميشود.
آلياژهاي ريختهگري پايه نيكل و فولادهاي زنگنزن را ميتوان با روشهاي مختلفي از جمله ريختهگري در ماسه، گريز از مركز، پوستهاي، قالب سراميكي و ريختهگري دقيق توليد نمود. آلياژهاي پايه نيكل كه بيشتر از 2 درصد عناصر فعال مانند آلومينيوم، تيتانيم و زيركنيم دارند نبايد در شرايط اكسيدكننده مانند هوا ذوب و ريختهگري شود.جدول زیر ترکیب شیمیایی آلیاژهای ریختگی پایه نیکل را بر اساس استاندارد ASTM A494 نشان می دهد.ریخته گری اینکونل 625 ، مونل 400، هاستالویC276، هاستالوی B2، نیکل خالص ZC-100، اینکونل 657 و آلیاژهای مشابه در شرکت اصفهان مالیبل با موفقیت بر اساس استانداردهای ASTMانجام شده و مدارک آن موجود می باشد.